Everything to know about trace heating
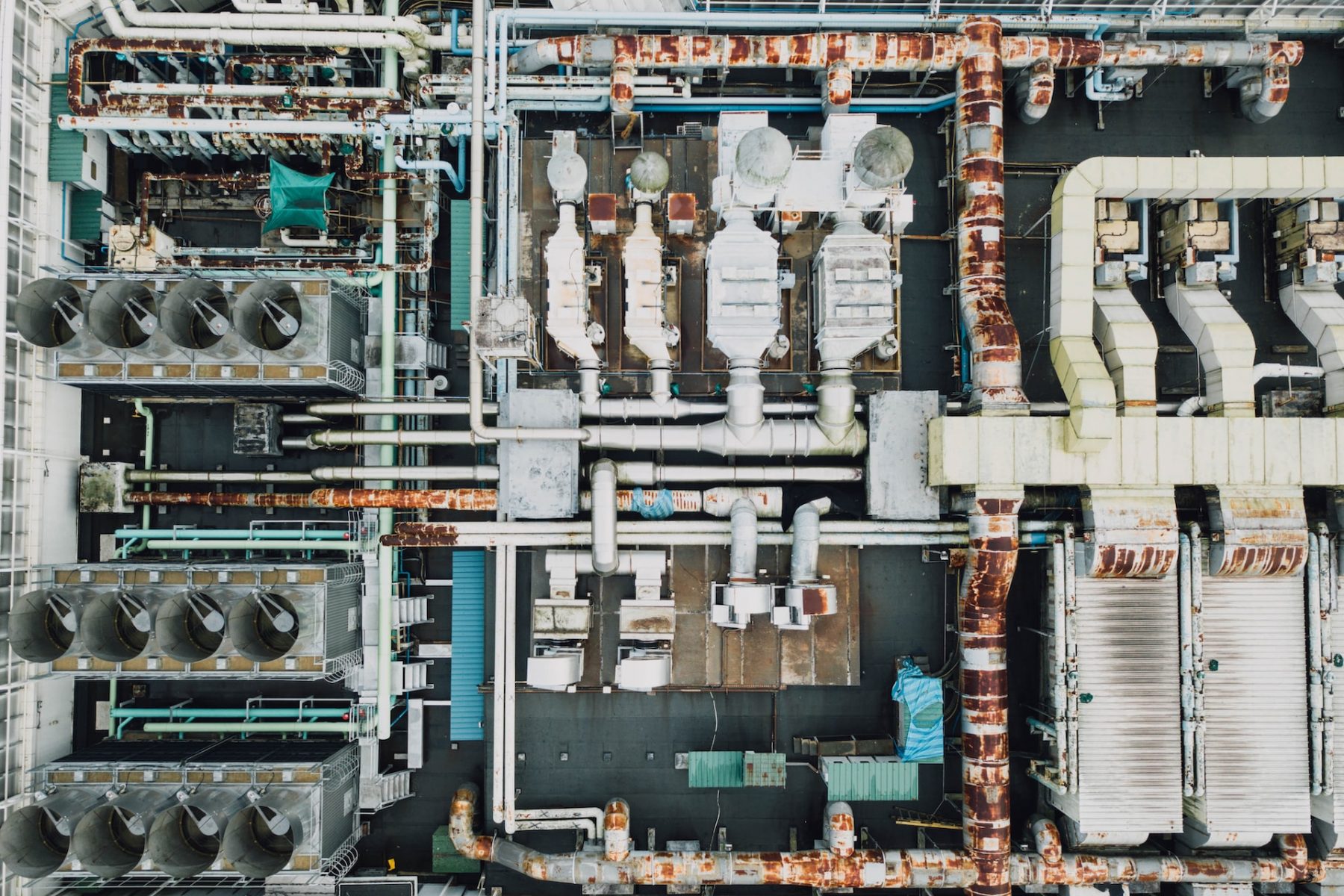
What is trace heating?
Trace heating is when the temperature of pipes and vessels is maintained or increased via specifically engineered cables. Trace heating products exist in response to the winter season when temperatures become very cold and can drop below freezing levels.
When this happens, businesses often look to trace heating as a solution to prevent their vessels and pipes from freezing during the coldest temperatures. This is when pipes can freeze over which might result in them bursting from the expanding ice applying too much pressure. So, the aim of a trace heating system is to stop frost from forming in water pipes by keeping temperatures at a certain level.
Also, heat tracing can be applied in processes that need temperature maintenance like insulating steam pipes. Another example is where certain liquids need to be kept at a specific temperature so they can be safely transported. In these cases, heat tracing can still be applied even without cold temperatures.
How does trace heating work?
Trace heating is done by connecting specifically engineered cables made from a resistance element to the vessel or pipe. The electric cables then have the job of process temperature maintenance by swapping heat loss with their power output. Ohm’s law dictates that connecting a voltage with a wire or cable will lead to a supply of power, which is then changed into heat energy by the heat tracing system.
Trace heating cables have two copper conductor wires that are the same length, which forms a heating zone with a resistance filament in position. With a supply of fixed voltage, a consistent wattage is generated which in turn heats up the zone. A thermostat monitors the trace heating cables to make sure that the correct amount of thermal energy is produced so the cable won’t underheat or overheat.
What are the different types of trace heating UK?
Series resistance trace heating
A series resistance heating cable is made up of a high-resistance wire that is usually insulated and enclosed within a protective cover. Thermal energy is created from the resistance of the wire when it is powered at s specific voltage level. The main benefit of a series resistance heating cable is that it often costs less than other options and is capable of maintaining very high temperatures for longer lines.
Therefore, series resistance trace heating cables are normally made to be a fixed length and can’t be shortened in the field. This is because any break or failure at any point along the line would lead the full cable to fail. So, series resistance trace heating cables are often used for longer pipeline heating procedures.
However, the circuit still needs to be monitored and controlled as the resistance material could melt because of overheating. Series resistance trace heating is normally put in place when long pipeline process heating is required, for example on the quay side of load pipes on oil refineries and along oil pipelines.
Constant wattage trace heating
The design for constant wattage trace heating cables includes a heating element that is wrapped around two insulated, parallel wires. There are several points throughout the trace heating cable that experiences constant wattage.
A notch is made in the insulation on opposite sides of the conductors. Then a small heating circuit is created by fusing the heating component to the exposed conductor wire and this is continued throughout the entirety of the cable. Next the parallel wires are separated from the grounding braid by an inner jacket.
A key advantage of constant wattage trace heating, compared to series resistance heating, is that the former can still work even in the event of an issue somewhere on the cable. In addition, the length of the cable can be altered on site thanks to its parallel functionality, this cannot be done with series resistance trace heating. It’s for this reason that a lot of businesses and industries ask heat trace specialists to install constant wattage trace heating, because of the flexibility you get with it.
Constant wattage trace heating cables always come with a thermostat when installed in order to monitor and regulate the power output of the cable. This is done to stop overheating and burning out, should the cable ever come into contact with itself.
Self-regulating trace heating
Self-regulating trace heating cables that can change depending on the temperature. On a basic level, when temperatures drop below a certain limit, the cable resistance will go down as well. However, the resistance of the cable will increase when the temperature goes above the specified level.
Self-regulating trace heating cables are made from two equal wires encased in a semi-conductive polymer. The polymer is typically made with carbon which stops the current from overflowing at increased temperatures. The carbon inside the polymer can expand or contract to generate different levels of resistance and heat energy output.
The length of the cables can be altered in the field. Also, the self-limiting capability of the cable enables it to be more energy efficient as it can lower its output at higher temperatures. Thanks to its feature of conserving energy when the temperature goes up, self-regulating cables can help businesses to save money as less power is used.
Additionally, these cables have better levels of safety which is particularly desirable in hazardous locations. This is because the power output of the cables won’t go above a certain level as output decreases when the temperature increases. So, it’s not possible for the cables to overheat, which could have been dangerous, especially in areas with flammable gases and vapours.
How can trace heating be applied?
Freeze protection
As previously mentioned, trace heating is often used to protect pipes and vessels from freezing by keeping the temperature at a set level above freezing point. This is done by providing heat energy to balance the level of heat lost through conduction. Keep in mind thermal insulation can only slow down the heat loss process, it can’t prevent it from happening completely. So, trace heating is a good solution to heat loss and frost protection.
Gutter and de-icing roof
Trace heating cables can be fitted to the roofs and in gutters to avoid the accumulation of ice or snow. Also, the cables function as a draining path for water from the melted ice to move through to stop overflowing in the rooftops and gutters.
Overflowing can have a negative effect on the structural integrity of buildings as it can lead to water soaking into cracks or joints. Additionally, the extra weight from the gathering of snow or melted ice can cause indentations and depressions on the rooftops and gutters. So, trace heating is key to preventing unwanted water build-up.
Anti-cavitation
Trace heating helps to lower the chance of cavitation occurring in pipes as heating a liquid makes it thinner and reduces its viscosity. The term cavitation refers to the development of vapour bubbles in a liquid caused by fast changes in pressure.
Shockwaves are created when the vapour bubbles or cavities in the liquid collapse or implode, which degrades the inside of the pipe over time. Also, cavitation can break up the flow of liquid within the pipes. So, putting heat tracing cables in place will lower the likelihood of cavitation as it helps to reduce the pressure difference in the liquid.
Conclusion
Thermal insulation doesn’t completely reduce heat loss, so heat tracing is needed for businesses to keep temperatures over a designated level. This is particularly important during the winter season when temperatures can go below freezing levels and frost heaving is likely to happen.
As professional trace heating suppliers, TRM can help you with your trace heating needs. Contact our team today to discuss your requirements.